Силикальцит – новый строительный материал
Известь применяется в качестве строительного вяжущего уже в течение тысячелетий, портландцемент же – лишь 50 лет. И несмотря на это, изготовление различных строительных деталей развивалось на базе портландцемента, а не извести. Бетон – новый искусственный камень и армированный бетон – продукция дальнейшего развития бетона, заняли господствующее место в строительстве. Говорится даже о бетонной эпохе. До настоящего времени из извести и песка изготовлялась лишь наипростейшая деталь – кирпич, производство которого началось всего 70 лет назад. Правда, теперь известь-песок или силикатный кирпич является наряду с обожженным из глины полноправным строительным кирпичом и обладает по сравнению с последним рядом преимуществ. Он также значительно дешевле глиняного кирпича. В течение последних десятилетий многие исследователи занимались вопросом возможности получения из извести и песка крупноразмерных строительных деталей.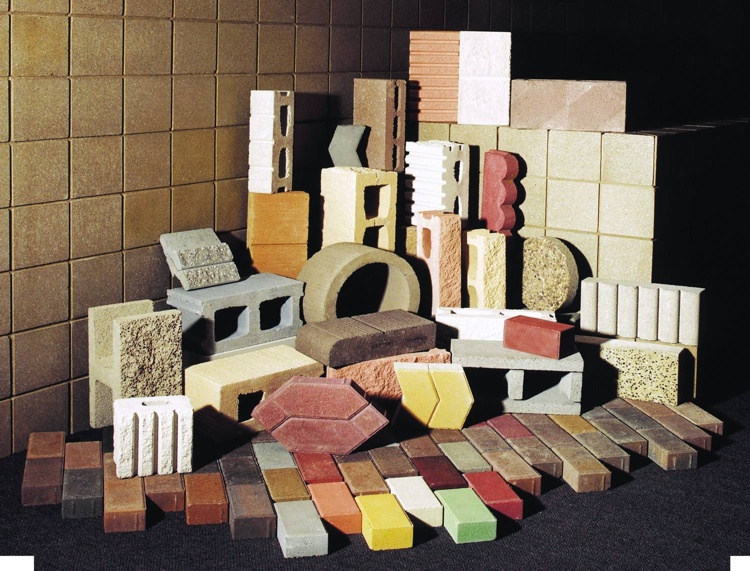
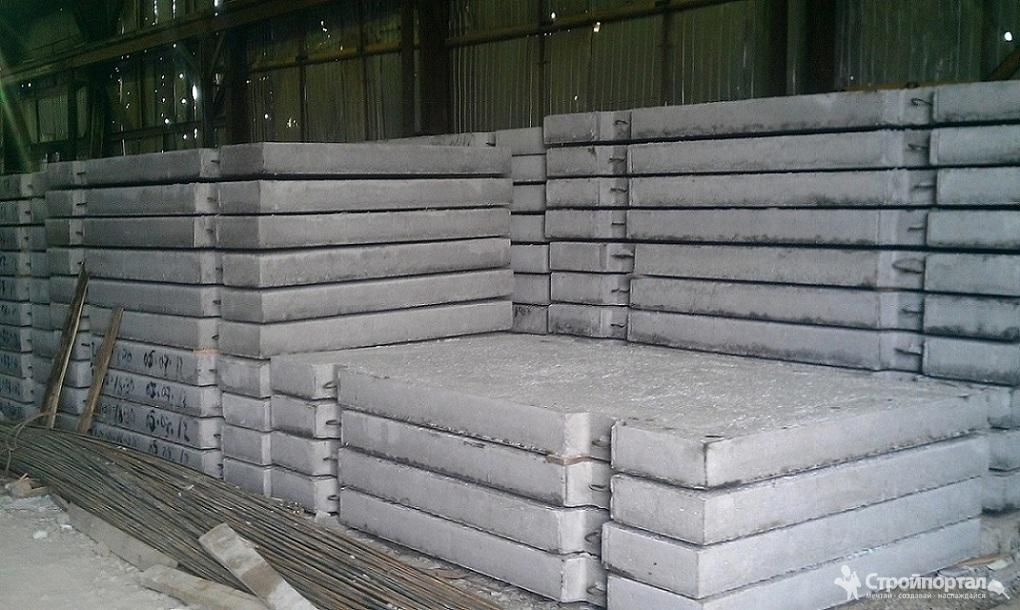
Эстонский силикальцит для защиты России
Еще в 1950-х годах эстонский ученый, изобретатель и хозяйственник Йоханес Рудольф Хинт разработал новый строительный материал — силикальцит. Получаемый из песка и известняка, широко распространенных материалов, этот материал оказался намного прочнее бетона.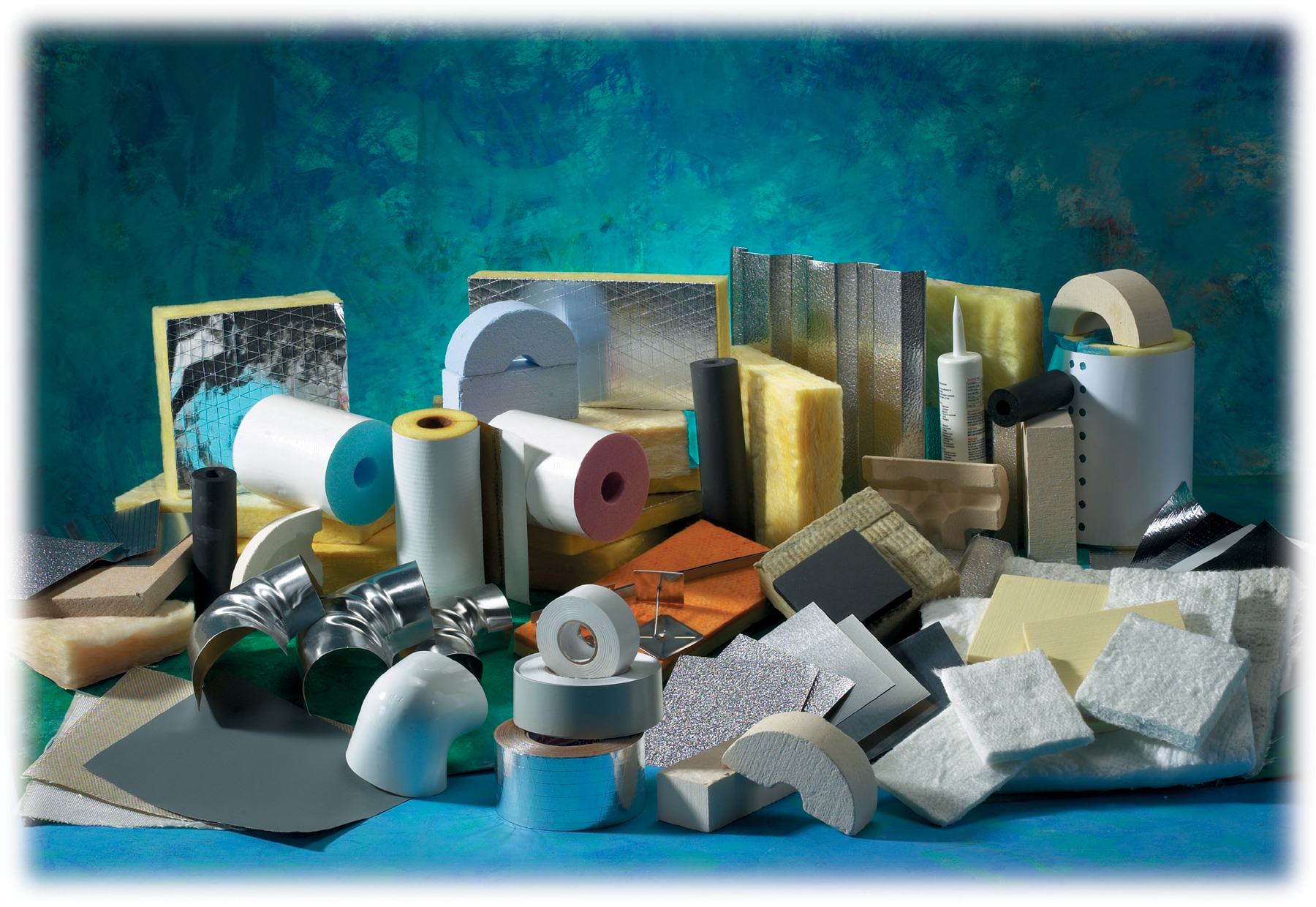
У Хинта была сложная биография. Он в 1941 году закончил Таллинский политехнический институт по специальности «инженер-строитель», но поддержал только что установленную в Эстонии советскую власть и даже вступил в компартию (его брат Ааду был коммунистом), потом руководил эвакуацией эстонской промышленности после начала войны, оставлен на подпольную работу. В 1943 году его арестовали немцы, но Хинту удалось сбежать из концлагеря из-под смертного приговора на лодке в Финляндию, там был снова арестован и помещен в лагерь военнопленных, где и просидел до конца войны с Финляндией. После войны он создал силикальцит, разработал технологию его производства и обработки, создал крупное предприятие и даже в 1962 году получил Ленинскую премию за эту разработку.
Конец этой истории был необычным и несколько неожиданным.
Дело Хинта было сильно политизировано, думается, потому, что, по здравом рассуждении, силикальцит должен был вытеснить цемент из строительства со всеми вытекающими отсюда последствиями реорганизации целой отрасли строительных материалов: закрытием цементных заводов, перепрофилированием и переоборудованием стройиндустрии, изменением стандартов и так далее. Перестановка кадров, вызванная введением силикальцита в широкое употребление, обещала быть настолько масштабной, что кое-кому показалось проще посадить инициатора этих нововведений, заодно запятнав и саму технологию.
Однако не станем копаться в деталях этой давно прошедшей истории. Силикальцит в любом случае интересен и имеет, на мой взгляд, очень хорошие перспективы в качестве строительного и конструкционного материала для военно-хозяйственных нужд. Именно с этой точки мы его и рассмотрим.
Преимущества силикальцита
Силикальцит представляет собой развитие силикатного кирпича, тоже производимого из песка и извести, известного еще с конца XIX века. Только силикатный кирпич весьма хрупок и его прочность на сжатие не превышает 150 кг/см2. Всякий, кто имел дело с ним, знает, что силикатный кирпич довольно легко раскалывается. Хинт с конца 1940-х годов искал способы увеличения его прочности и такой способ нашел. Если не вдаваться в технические тонкости, то суть дела состояла в совместном размоле песка и извести в дезинтеграторе (особый вид мельницы, состоящий из двух кругов, вращающихся в противоположных направлениях, на которых в три кольцевых ряда установлены стальные пальцы; размалываемый материал сталкивается с пальцами и дробится от этих соударений в мелкие частицы, размер которых можно регулировать).
Дезинтегратор в разрезе (иллюстратор убрал защитный кожух, чтобы показать устройство мельницы). Этот тип мельницы известен давно и разрабатывался еще в XIX для более качественного помола муки. Вот умели же тогда рисовать грамотные и доходчивые иллюстрации!
Песчинки сами по себе довольно плохо соединяются с частицами извести, поскольку они покрыты слоем карбонатов и окислов, но размол сбивает с песчинок эту корку, а также раскалывает песчинки на более мелкие части. Свежие сколы на песчинках быстро облепляются частицами извести. После размола в смесь добавляют воды, формуют изделие и пропаривают в автоклаве.
Такой материал оказался значительно прочнее бетона. Хинт получал материал с прочностью на сжатие до 2000 кг/см2, тогда как самый лучший бетон имел прочность до 800 кг/см2. Резко увеличилась прочность на растяжение. Если у бетона В25 она составляет 35 кг/см2, то у силикальцитных железнодорожных шпал прочность на растяжение достигала 120-150 кг/см2. Эти показатели были достигнуты уже в конце 1950-х годов, и сам Хинт считал, что это далеко не предел, и можно достичь прочности на сжатие, как у конструкционной стали (3800-4000 кг/см2).
Как видим, материал очень хорош. Высокая прочность деталей позволяет сооружать малоэтажные здания совершенно без применения арматуры. В Эстонии было построено довольно много зданий из него, и жилых (общей площадью 1,5 млн. кв. метров), и административных (бывшее здание ЦК КПЭ, ныне здание МИД Эстонии). Помимо этого, силикальцитные детали армируются так же, как и бетонные.
Откосы канала Москва-Волга были облицованы силикальцитными плитами.
С экономической точки зрения силикальцит намного лучше цемента. Во-первых, тем, что при его изготовлении не используется глина (добавляемая при изготовлении цементного клинкера). Песок и известняк (или другие породы, из которых можно получить известь — мел или мрамор) есть почти везде. Во-вторых, тем, что не нужны грандиозные вращающиеся печи для обжига клинкера; дезинтегратор и автоклав гораздо компактнее и требуют меньше металла. Хинт однажды даже оборудовал плавучий завод на списанном судне. Дезинтегратор установили на палубе, а автоклав в трюме.
Все эти обстоятельства имеют большое значение для воюющей экономики. Военная обстановка как раз предъявляет большой спрос на дешевый и прочный строительно-конструкционный материал.
Силикальцит на войне
Как можно обрисовать военно-хозяйственное применение силикальцита? Вот таким образом.
Первое. Война, вопреки распространенным представлениям, связана с большими строительными работами. Речь идет не только и не столько о сооружении укреплений и защищенных огневых точек, хотя и это также имеет значение. Укрепленная прочным материалом огневая точка гораздо лучше, чем древо-земляная или вовсе без какого-либо укрепления. К силикальциту хорошо применима технология сооружения сборных железобетонных огневых точек (ЖБОТ), разработанная в начале Великой Отечественной войны. Из силикальцита можно точно так же изготовить блоки, из которых складывается дот. Но есть разница. Сырье для силикальцита можно заготовить поблизости от места строительства и переработать в готовые изделия на мобильной установке (дезинтегратор очень компактен и легко устанавливается на грузовике, а также можно разработать мобильный автоклав; не говоря уже об установке железнодорожного исполнения). Это существенно ускоряет строительство и делает его менее зависимым от дальнего подвоза материалов.
Строить в военных условиях нужно много чего: жилье, новое и восстанавливаемое, цеха для разного рода производств, дороги, мосты, различные объекты. Многие считают опыт Второй мировой войны устаревшим, но если начнется еще одна крупная война, то придется к нему обратиться, поскольку строители с обеих воюющих сторон работали тогда с максимальным напряжением. И все военные строительные программы страдали от острой нехватки цемента, от проблемы, разрешаемой как раз силикальцитом.
Второе. Высокая прочность изделий из силикальцита, формуемых прессовкой из очень мелко перемолотой смеси песка и известняка и обрабатываемых в автоклаве, позволяет использовать этот материал для производства некоторых деталей техники и боеприпасов. Железобетонным танком теперь уже никого не удивишь; подобный способ кустарного бронирования получил весьма широкое распространение. Реализуемость этого подхода была доказана еще в проекте Т-34ЖБ, опытного танка с железобетонной защитой, своего рода подвижного дота.
Т-34ЖБ. Конкретно эта идея навесить на танк дополнительные железобетонные плиты не слишком удачна. Целесообразнее переделать корпус танка целиком.
Силикальцит позволяет сделать такую защиту более прочной и более легкой, чем у железобетона, с сохранением всех преимуществ стального или волоконного армирования. При производстве силикальцитных изделий с прочностью конструкционной стали становится возможным даже заменять ими некоторые стальные части машин. Например, рамы у грузовых автомобилей.
Далее, есть разновидности пеносиликальцита, которые легче воды и обладают плавучестью. Потому силикальцит различных марок, легкий и плавучий, а также прочный и твердый, может служить конструкционным материалом для строительства паромов, судов, понтонов, в том числе самоходных, разборных плавучих мостов и т. п. Если вспомнить экстравагантную идею строительства грандиозных «плавучих островов», с помощью которых можно переплыть океан и высадиться на территории нашего главного вероятного противника, то тут силикальцит открывает большие перспективы и возможности, чем железобетон.
Наконец, из силикальцита, по немецкому примеру, можно изготовлять корпуса реактивных снарядов. Железобетонные реактивные снаряды изготовлялись в Германии в конце войны и показали себя столь же хорошо, как и стальные. Силикальцитовая труба может быть прочнее железобетонной, а стало быть, легче.
Если фотографий немецкого реактивного снаряда из железобетона найти не удалось, то вот попалась другая интересная фотография — немецкий 240-мм миномет Albrecht времен Первой мировой войны, сделанный из дерева. Раз можно сделать вполне боеспособный миномет из дерева, то почему нельзя сделать миномет из силикальцита?
Смысл этих мер состоит в том, чтобы заменить сталь, которая в ходе большой войны станет остродефицитным материалом, на более дешевый и гораздо более доступный по сырью и энергозатратам материал. На мой взгляд, давно уже пора всерьез задуматься о том, чтобы в производстве боевой техники, оружия и боеприпасов заменить как можно больше стали на различные силикатные материалы (не только силикальцит, но и керамику, а также разнообразные композиты), подходящие по свойствам. Если с ресурсами железной руды у нас уже становится трудно (Криворожское месторождение теперь у вероятного противника, другие месторождения сильно истощены, так что теперь металлургические компании налаживают переработку ильменитовых песков), то вот с сырьем для производства силикатных материалов проблем нет, они почти не ограничены.
У меня получился очень краткий и беглый обзор военно-хозяйственных возможностей силикальцита, без детального обоснования и анализа конкретных примеров. Думаю, что если изучить вопрос достаточно глубоко, то получится целая книга (весьма пухлая по объему). У меня есть предвкушение, основанное на опыте изучения военной экономики, что силикальцит может революционизировать военно-промышленную сферу и дать военному хозяйству мощный источник материалов.
Создание новых строительных материалов на основе силикацитов
1. Актуальность проблемы.
Современное производство строительных материалов основано на применении традиционных технологий использующих цемент. Запасы сырья для производства цемента в мире стремительно тают, что приводит к удорожанию самого цемента и стоимости строительства.
Концептуально содержание научно-исследовательских и опытно конструкторских работ перелагаемых в рамках проекта состоит в комплексном применении и совершенствовании следующих технологий:
- Технологии получения бетона на основе силикальцита без дорогостоящего цемента
- Технологии активации строительных растворов при помощи структурированной воды и созданных на ее основе коллоидных растворов.
- Технологии активации строительных смесей в жидкой вязкой среде.
Другими
словами опытно внедренческая деятельность в рамках проекта направлена на
снижение себестоимости производства строительных материалов и удешевлению
строительных объектов.
2. Обзор известных технологий в области применения силикальцитов в строительных технологиях.
Опыты и эксперименты И. Хинта и его последователей.
Идея активации силикальцитов принадлежит выдающемуся советскому ученому Йозефу Хинту, который начал эксперименты по активации силикальцитов еще в 1947 году. В 80-х годах прошлого века
И. Хинтом в работе «УДА — технология: проблемы и перспективы», Таллин » Валгус ” 1981 были сформулированы основные теоретические основы дезинтеграции. В работе акцентировано, что дезинтеграция компонентов веществ не только их измельчение, но и механическая активация продуктов интеграции (насыщение энергией) за счет огромных скоростей соударений, позволяет сделать заключение об универсальности технологии для многих направлений производств, использующих измельчение исходных компонентов. Она так и названа УДА – универсальная дезинтеграция и активация большой механической энергией.
Продолжателем дела И. Хинта в полной мере является МП
«ТЕХПРИБОР», города Щекино Тульской области, совершенствующее технологии
производства бетонных смесей и серийно
производящее широкую номенклатуру оборудования, основанного на УДА-технологии. Авторское право на решения МП «ТЕХПРИБОР» защищено патентами РФ. Наиболее
перспективны разработки Ударно-центробежная шаровая мельница — классификатор
(УЦШМК) «ТРИБОКИНЕТИКА-1000» Дезинтегратор «ГОРИЗОНТ-ДОМИНАТОР-9.5», Дезинтеграторный пульверизатор «ГОРИЗОНТ 3000 МК-АГ»,
Метод селективной дезинтегаторной активации портландцемента (СДАП). Метод СДАП
использует низкосортный портландцемент как сырье для получения качественного
цемента в дезинтеграторах на площадях заводов ЖБИ или строительных площадках,
тем самым децентрализует производство цемента, не затрагивая реорганизацию
изношенного и затратного цементного производства, проблемы, не решаемой в
рамках Государственной политики и соответствующих Государственных программ.
К сожалению, развитие методов и технологий получения
силикальцита на настоящее время затормозилось. Сырьем для смесей силикальцита
является повсеместно распространенные материалы – песок и известняки осадочных
пород. Возможно, проблемой являются организационные вопросы технологии, которые
должны включать разработку добычи компонентов сырья и щебня или поставки их по договору, оснащения строительной
площадки емкостями для хранения сырья и компонентов смеси силикальцита,
оснащения оборудованием для дробления
известняка с целью подготовки его для подачи в дезинтегратор, оснащения
другим оборудованием технологической цепи – дезинтегратором, смесителем для
приготовления цементного раствора, а также приборами и оборудованием для испытания
контрольных образцов бетона на прочность для контроля качества процесса
бетонирования строительного объекта. Представленный выше перечень оборудования
технологической цепочки бетонирования достаточен для малоэтажного котеджного
строительства, но для объектов дорожного строительства или специальных и высотных объектов естественно должен быть дополнен серийными или спроектированными
и изготовленными машинами, оснасткой и
приспособлениями.
Технологии дизентеграции в жидкой вязкой среде.
Коллективом ученых ООО «НРБТ» совместно с учеными Московского государственного университета технологий и управления с 2009 года ведутся работы по созданию нового строительного материала на основе нанотехнологий. Проведенные до сегодняшнего дня исследования показали, что чем мельче дробление частиц, входящих в исходные материалы, тем большая энергия сцепления возникает в получаемом материале.
В
результате использования метода гидродинамической деструкции и реструктуризации
в вязкой жидкой среде, нами получены частицы окиси кремния (SiO2) и
известняка (CaCO) с
характерными размерами от 0,8 мкм до
0,05 мкм. Полученный строительный
материал, состоящий из столь малых частиц,
обладает уникальными прочностными
и эксплуатационными характеристиками. Характерной особенностью нового
строительного материала является то, что
в его состав не входит цемент, либо, по
второму варианту, его количество незначительно, что значительно уменьшает
себестоимость полученного бетона. Первые образцы такого материала получены в
нашей лаборатории:
Используя способ вихревого гидродинамического дробления [3], на основании анализа экспериментальных работ в 2009 году в МГУТУ с целью интенсификации измельчения и гомогенизации в вязкой жидкой среде нами был создан дезинтегратор ДК-1.
Опыты, проведенные на дезинтеграторе ДК-1, показали,
что в условии генерации микровихревых гидродинамических структур в вязкой среде
не только происходит измельчение твердых частиц, входящих в состав суспензии,
но и происходит дезинтеграция молекул с образованием сверх активных нано частиц,
время жизни которых определяется временем нахождения этих частиц в микро вихре. По нашим оценкам время жизни микровихрей составляет единицы микросекунды. За
это время происходит процесс дезинтеграции молекулы и ее реструктуризации. На
месте разрыва молекулы образуются свободные молекулярные связи, к которым и
присоединяются свободные ионы из суспензии.
Данный метод позволяет резко снизить энергозатраты на производство и повысить прочностные характеристики силикальцитов. Не менее важно и то, что затворение растворов структурированной водой так же ускоряет процесс схватывания растворов и его прочностные характеристики.
Технологии сушки в СВЧ полях.
Изменение свойств строительных растворов может происходить и в процессе сушки в СВЧ полях. Первые эксперименты в этой области проведены партнерами учеными МГУТУ и МИЭМ.
Комбинация
этих трех комплексов технологий позволяет в рамках проекта провести
исследования и опытно-конструкторские работы всего процесса производства
строительных материалов и создания линейки строительной техники значительно, в
разы, снижающей затраты на строительство.
Безцементная технология строительства
Безцементная технология строительства.
Безцементная технология строительства.
На дворе 20 век, а я предлагаю вернуться более чем на 100 лет назад. Это будет путешествие назад в Будущее.
Приоратский дворец имеет еще одно название — Земляной дворец. Это второе его наименование раскрывает не менее примечательную, чем художественно-архитектурная, строительно-инженерную особенность здания. Дело в том, что дворец, стена и кухня построены Н.А. Львовым с применением «землебита» — прессованной и просушенной земли. Ограда и сторожки у ворот построены из землебитного кирпича, размером 15х30 см. Причём стены ограды сложены, как обычно на извести.
Это уникальное строение было сооружено на болоте в 1799 году. Смесь извести песка и земли прочнее бетона! Кругом болото, поэтому в качестве земли следует ожидать торф. Землю набивали в специальные станки — опалубки и прессовали. Хорошо просеянный, освобожденный от растительных примесей, слегка увлажненный материал, засыпали слоем около десяти сантиметров и утрамбовывали до толщины шести сантиметров. Далее засыпали следующий слой, трамбовали и так слой за слоем до карниза. Для связки между слоями использовали известковый раствор. Н.А. Львов подобрал такой состав грунтомассы, что по прочности она по сей день соперничает с железобетоном. Объемный состав этой грунтомассы следующий: гравий крупностью от 3 до 7 мм — 4%; песок — 58%; пыль (мелкая земля) — 20%; глина — 18%. Органические примеси не добавлялись. Прочность землебита у Львова через 20-30 лет после возведения здания составила 10-12 МПа, хотя цемент в состав грунтомассы не вводился. Следует отметить конструктивные особенности подпорной стены. В ее основание горизонтально положены бревна диаметром 27 сантиметров, пропитанные особой каменноугольной смолой, изобретенной Львовым. Над бревнами идет ряд нещадных плит. На плитном слое сложены из блоков известнякового камня две стены — вертикальная задняя и наклонная передняя. Между ними засыпана забутовка — камень и известь. Поверх подпорной стены устроен изоляционный слой из глины, смешанной с соломой.
В очищенной от штукатурки стене видна «землебитная» кладка. Фото нашего времени.
Питер по сей день стоит на деревянных сваях. Без доступа воздуха дерево каменеет.
При запаривании смесей извести — песка — воды в результате взаимной химической реакции исходных материалов возникает вяжущее гидросиликат кальция с общей формулой: x CaO y SiO 2 z H 2 O.
Торф содержит лигнина (негидролизуемый остаток) 3-20%. Лигнин применяется, как наполнитель для пластмасс и композиционных материалов, в качестве связующего для композиционных материалов (лигноплиты и т.п.) и добавки в асфальтобетоны. Причем в хвойных породах лигнина максимальное количество.
Из торфа успешно изготовляются торфоблоки.
Высокое сопротивление теплопередаче, в пределах 0,047-0,08.
Массовость распространения по территории РФ исходного материала для его производства. 53% мировых запасов торфа на территории РФ в регионах с наибольшей плотностью населения и с наихудшими показателями по удовлетворённости граждан в жилье.
Связующим в торфоблоке является сам торф (лигнин). В качестве наполнителя можно применять любые материалы растительного происхождения такие как: опилки, льняную и конопляную костру, измельченную солому и т. д.
При кирпичном строительстве снижается стоимость стены в два раза, теплопотери соответственно — в три раза. Вес 1-го м. куб. в пределах 0,40 0,45 тонн. При кладке не требуется цемент.
Современное производство требует пропаривание того же бетона и торфоблоков, но дворец — то строился с сушкой на открытом воздухе.
В технологии возведения землебитного дома упоминаются колотушки. Т.е. наличие продольных волн. Смотри статью торсионные поля. При применении продольных волн ускоряются все химические реакции, увеличивается прочность бетона, значительно сокращается период схватывания бетона. Булатную сталь изготавливали подобным же методом. Кузнецы ударяли по стальной заготовке через стальную проложку молот! Вроде бы ничего, а свойства материала меняются в разы.
Бе з цементная технология строительства.
Cовместная обработка извести и песка в специально переконструированном дезинтеграторе создает зерна песка и известково-песчаные смеси с новыми свойствами. Хинт назвал свой материал СИЛИКАЛЬЦИТ. В итоге из простой извести и простого песка выпускались изделия марочностью М3000 в серийном производстве, и до М5000 в опытно-промышленном. Известь химически взаимодействует с песком, поэтому для ускорения реакции смесь следует подвергнуть вибрации дроблению в торсионном поле.
Безцементная технология строительства.
Учитывая все это, понятно, почему при производстве на заводах равной мощности силикальцит, по меньшей мере, в 2 раза дешевле бетона. Это означает, что завод, построенный за сумму, в 2,5 раза меньшую, дает постоянно из года в год более качественную. чем бетон, и в 2 раза более дешевую продукцию.
Далее При равных показателях прочности бетонные изделия примерно на 30% тяжелее силикальцитных. Например, высоко прочный силикальцит, имеет объемный вес только 1900 кг/м3. Бетон с прочностью в 5 раз меньшей имеет объемный вес не меньше 2200 кг/м3. Эта большая разница в весе конструкции существенно снижает расходы на транспорт и позволяет за счет удешевления фундаментов домов и несущих конструкций получить немалую экономию.
Приняв во внимание, что в производстве силикальцита требуется, в основном, лишь единственная машина — агрегат для приготовления смеси, можно организовать также подвижные, экономично работающие заводы.
Перечислим основные преимущества СИЛИКАЛЬЦИТА.
1. Технологичность. Силикальцит изготовляется из 90% песка и 10% извести. В бетоне 88% песка, гравия или щебня и 12% извести.
2. Силикальцит со временем твердеет (каменеет). Все другие материалы только разрушаются.
3. Экологичен. Силикальцитные технологии несоизмеримо экологичнее цементных заводов.
4. Выше прочность. В первые годы производства силикальцита были изготовлены образцы с прочностью свыше 1000 кг/см2. Прочность же бетона за полтораста лет повысилась лишь до 500 кг/см2.
5. Водопроницаемость плотного силикальцита в тысячу раз меньше, чем у плотного бетона.
6. Кислотоустойчивость. Силикальцит хорошо противостоит воздействию даже 5%-го раствора соляной кислоты, от бетона же в этом случае через несколько дней остаются лишь зерна песка и гравия.
7. Ниже плотность. При равных показателях прочности бетонные изделия примерно на 30% тяжелее силикальцитных.
8. Низкая стоимость производства. Стоимость силикальцитного завода в 2,5 раза ниже стоимости бетонного завода такой же мощности вместе с организацией производства необходимого для работы завода количества цемента.
9. Ниже расход материалов. На изготовление 1 м3 силикальцитных изделий затрачивается вдвое меньше извести, чем цемента на изготовление такого же количества бетона. При одинаковой степени механизации же производство цемента вдвое дороже извести. Отсюда уже разница в 4 раза.
10. Ниже требования к сырью. Для производства силикальцита употребляется любой дешевый природный песок, производство же бетона требует особенно чистого песка с подходящим зерновым составом и хорошего щебня.
11. Дешевле бетона. При производстве на заводах равной мощности силикальцит, по меньшей мере, в 2 раза дешевле бетона. Это означает, что завод, построенный за сумму, в 2,5 раза меньшую, дает постоянно из года в год более качественную. чем бетон, и в 2 раза более дешевую продукцию.
12. Не меняет размера при затвердевании. Силикальцит как бы создан для производства индустриальных деталей. Даже наиболее крупноразмерные детали затвердевают в автоклаве без напряжений и не изменяют своих размеров. Обычный же бетон при твердении уменьшается в объеме.
Но, посмотрите ГОСТ 25485-82 в таблицу названий разновидностей ячеистых бетонов (таблице 2) и обратите внимание на приписку снизу таблицы.
Нет ГОСТа на материал — значит, нет и материала. Такова российская действительность. Но убить истинные ценности не просто. В каждом мешке с импортной сухой строительной смесью присутствует частичка души Йоханеса Хинта.
Электропластический эф ф ект в метал л ах.
Маленько физики. У становлен электропластический эффект в металлах и доказана возможность его применения для практических целей. Открытие этого эффекта привело к более глубокому пониманию механизма пластической деформации, расширило представление о взаимодействии свободных электронов в металле с носителями пластической деформации-дислокациями. Появилась возможность управлять механическими свойствами металлов, в частности, процессом обработки металлов давлением. Например, деформировать вольфрам при температурах не превышающих 200 гр.С и получить из него прокат с высоким качеством поверхности. В экспериментах с импульсным током было найдено, что электрический ток увеличивает пластичность и уменьшает хрупкость металла. Если создать хорошие условия теплоотвода от деформируемых образцов и пропускать по ним ток высокой плотности 10 4 -ой 10 6 -ой а/см 2. то величина эффекта будет порядка десятков процентов. Электрический ток вызывает также увеличение скорости релаксации напряжений в металле и оказывается удобным технологическим фактором для снятия внутренних напряжений в металле . Электропластический эффект также линейно зависит от плотности тока (вплоть до 10 5 -ой а/см 2 ) и имеет большую величину при импульсном токе, а при переменном вообще не наблюдается. Видна связь явления разупрочнения металла при сверхпроводящем переходе с электропластическим эффектом. В этом и другом случае происходит разупрочнение металла. Однако, если в первом случае в основе явления лежит уменьшение сопротивления движению и взаимодействию дислокаций при устранении из металла газа свободных электронов,во втором случае причиной облегчения деформации является участие самого электронного газа в пластической деформации металла. Электронный газ из пассивной и тормозящей среды превращается в среду, имеющую направленный дре йф и поэтому ускоряющую движение и взаимодействие дислокаций (или снижающую обычное электронное торможение дислокаций) . Этот эффект уже находит свое применение на практике: Способ снижения прочности металлов, например,при пластической деформации при котором через заготовку пропускают электрический ток отличающийся тем, что с целью снижения прочности металла при сохранении его низкой температуры, к заготовке прикладывают импульсы тока плотностью преимущественно 10 а/см 2. с частотой подачи 20-25Гц.
Ударные волны от тока исследовал еще Тесла. Он их назвал радиантными. Эти волны ионизируют воздух, над свободным концом катушки возникает коронное свечение. Сейчас это излучение называют еще торсионным.
Связь электропроводности с деформацией. В 1975 году зарегистрировано открытие: обнаружена зависимость пластической деформации металла от его проводимости. При переходе в сверхпроводящее состояние повышается пластичность металла. Обратный переход понижает пластичность. Напомним, что макроскопическая пластическая деформация осуществляется перемещением большого количества дислокаций, способность же кристалла оказывать сопротивление пластической деформации определяется их подвижностью. Эффект наблюдался на многих сверхпроводниках при различных способах механических испытаний. В экспериментах было обнаружено значительное повышение пластичности металла /разупрочнение/ при переходе его в сверхпроводящее состояние. Величина эффекта в некоторых случаях достигла нескольких десятков процентов.Детальное изучение явления разупрочнения привело к выводу,что «виновником» его следует считать изменение при сверхпроводящем переходе тормозящего воздействия электронов проводимости на дислокации. Силы «трения» отдельной дислокации об электроны в несверхпроводящем металле резко уменьшаются при сверхпроводящем переходе.Таким образом, обнаружена прямая связь механической характеристики металла, его пластичности, с чисто электронной характеристикой -проводимостью. Главный вывод- электроны металлов тормозят дислокации всегда .Сверхпроводящий переход помог выявить роль электронов и позволил оценить электронную силу торможения. Но переход в сврхпроводящее состояние- не единственная возможность влиять на электроны. Этому служит магнитное поле, давление и т.д . Ясно, что такие воздействия должны изменять и пластичность металла, особенно, когда электроны — главная причина торможения дислокаций. Магнитное поле ( импульсное ) в сочетании с низкой температурой способны изменять буквально все свойства вещества: теплоемкость, теплопроводность, упругость, прочность и даже цвет . Появляются новые электрические свойства. Превращения происходят практически мгновенно- за 10 11 -ой и 10 12 -ой сек. Исходя из экспериментов ожидают использования новых эффектов в обычных условиях.
Генератор торсионного поля Курапова С.А.
При воздействии торсионного поля на жидкий металл, он приобретает более мелкую структуру, повышается его прочность. В генераторе Акимова торсионное поле создает ферритовый сердечник. Феррит, похоже, создает знакомые эфирные колебания. При воздействии торсионным полем, на металл проходящим через редкоземельные материалы, металл приобретает частично свойства этого материала. По-видимому, при остужении металла, ему передается частота вибраций свойственная только редкоземельному материалу.
Например, чтобы получить определенного качества чугун, обыкновенный чугун отжигают в течение 120 часов. При воздействии торсионного поля чугун необходимого качества, имеющий структуру пластического графита, получают сразу же.
Воздействие торсионного поля увеличивает ударную вязкость легированных металлов. С его помощью удалось передать свойства никеля в металл для производства буровых штанг, не добавляя в него никель. Это было достигнуто следующим образом. Взяли пластинку никеля, поставили ее на пути прохождения луча, и ударная вязкость возросла на 50-52% при сохранении тех же прочностных характеристик. Поскольку завод производит 55 тыс. изделий, то это — огромная масса металла, и очень большая экономия дорогостоящего никеля. В некоторых случаях ударная вязкость легированных металлов возрастала в 3-4 раза.
экспериментально доказано украинскими учеными В.П. Майбородой и И.И. Тарасюком при воздействии торсионным генератором на кристалл типа кадмий-ртуть-теллур. При этом наблюдалось изменение магнитных свойств на величину, требующую в миллион раз больше энергетических затрат, чем было затрачено на работу торсионного генератора. интенсивность торсионного поля не зависит от удаленности от источника поля и обладает исключительной проникающей способностью в любых природных средах.
Метод получения ударных волн.
Ударные волны распространяются в металле с огромной скоростью, передавая ее заготовке, содрагая электроны связи. Материал получается с более мелкой структурой зерна, более прочным и пластичным . Смотри также статью Высокоэффективная энергетическая установка.
Вывод: с помощью вибрации и продольных волн мы значительно снизим себестоимость продукции и значительно повысим прочность и пластичность.
С уважением Бегенеев Сергей.
30.01.2017производство силикальцита — Материалы и свойства
Автор Admin На чтение 2 мин. Просмотров 78 Опубликовано
Силикальцит — известково-песчаный бетон, составляющие которого обработаны в дезинтеграторах.
В дезинтеграторах песок подвергается «раскалыванию» и «шелушению», что увеличивает удельную поверхность его, улучшает «активность» и гранулометрический состав. Возникающие в дезинтеграторе воздушные потоки способствуют плотному обволакиванию поверхности зерен песка известью, что улучшает их взаимодействие при твердении.
Дезинтегратор состоит из двух дисков-корзинок диаметром до 2,5 м, насаженных на валы, вращающиеся в противоположные стороны со скоростью 1000—1500 об/мин. Корзинки снабжены двумя-тремя концентрическими рядами цилиндрических пальцев, расположенных так, что каждый ряд одной корзинки свободно входит между двумя рядами другой (рис. 8). Производительность дезинтегратора при двигателе мощностью 48 кет около 4.5 г смеси в час.
К форме зерен и гранулометрическому составу песка при дезинтеграторном способе производства требований не предъявляется; содержание S1O2— не менее 65%. глины — до 10%
Известь должна соответствовать ГОСТ при активности не менее 60% (расход ее зависит от активности). Влажность гидратной извести не должна превышать 15%. Молотая негашеная известь должна давать на сите OfI мм остаток не более 15% (добавляется в смесь в минимальном количестве).
Состав известково-песчаных смесей, по данным опытного завода в Таллине, приведен в таблице 74.
Схема дезинтегратора.
Таблица 74 — Состав известково-песчаных смесей (по данным И. Хинта)
Силикальцитные детали | Удельная поверхность песка в смеси см2/г | К-во гидратн. извести в смеси | К-во молотой негашеной извести в смеси %, СаО | Формовочная влажность % |
Вибрированные армированные и неармированные 1750 кг/м3 | 250-350 | 9-10,5 | — | 14-15 |
350-450 | 10,5-12 | 15-16 | ||
450-550 | 12-13,5 | 16 – 17 | ||
550- 650 | 13,5-15 | 17-18 | ||
Литые армированные и неармированные | 250 — 350 350 — 450 | 7—8,5 8,5-10 | 3 | 22-23,5 23,5-25 |
450-550 | 10—11,5 | 26-28 | ||
Пеносиликальцитные объемным весом 600—1800 кг/м3 | 600-700 — | 4-5 4-5 | 11-12 | 32-34 |
700-800 | 10,5-12 | 12- 13,5 | 34-36 | |
Черепица при ручном трамбовании, на гидравлическом прессе под давлением 100 кг/см2 | 300—400 400-500 350-450 450—550 | 10,5-12 12,5-13.5 12-13,5 18-15 | 11-13 13 15 8 9 |
Изделия из таких смесей имеют следующие показатели: | ||
Литой силикальцит | 1,5—1,6 т/м3 | 170-200 кг/см2 |
Вибрированный | 1,7—1,85 . | 250-400 . |
Прессованный | 1,8-1,95 . | 400-600 . |
Пеносиликальцит | 1.1-1,3 . | 110-170 . |
0,9—1.0 | 60- 90 . | |
0,6 | 30 |
Морозостойкость силнкальцитных изделий примерно такая же, что и для силикатных.
автореферат диссертации по строительству, 05.23.05, диссертация на тему:Получение и свойства автоклавного пенобетона на композиционной основе по резательной технологии
Автореферат диссертации по теме «Получение и свойства автоклавного пенобетона на композиционной основе по резательной технологии»
мот*»!«
на правах рукописи
МАРТЫНОВА Валентина Дмитриевна
ПОЛУЧЕНИЕ И СВОЙСТВА АВТОКЛАВНОГО ПЕНОБЕТОНА НА КОМПОЗИЦИОННОЙ ОСНОВЕ ПО РЕЗАТЕЛЬНОЙ ТЕХНОЛОГИИ
Специальность 05.23.05 — Строительные материалы и изделия
Автореферат диссертации на соискание ученой степени кандидата технических наук
Санкт-Петербург 2003
Работа выполнена в Государственном образовательном учреждении высшего профессионального образования «Петербургский государственный университет путей сообщения Министерства путей сообщения Российской Федерации» на кафедре «Инженерная химия и защита окружающей среды» и на научно-производственной базе Университета путей сообщения.
Ц
Научный руководитель -доктор технических наук, профессор СВАТОВСКАЯ ЛАРИСА БОРИСОВНА
Официальные оппоненты: доктор технических наук ШАНГИНА НИНА НИКОЛАЕВНА;
кандидат химических наук, доцент СЫЧЕВ МАКСИМ МАКСИМОВИЧ
Ведущее предприятие — ООО «ЦЕМТЕХ», Санкт — Петербург
Защита состоится 3 июля 2003 г. в 13.30 на заседании
диссертационного Совета Д 218.008.01 в Государственном
образовательном учреждении высшего профессионального образования
«Петербургский государственный университет путей сообщения •>
Министерства путей сообщения Российской Федерации» по адресу:
190031, Санкт-Петербург, Московский пр. 9, ПГУПС, ауд. 3-237
С диссертацией можно ознакомиться в библиотеке Университета.
Автореферат разослан 29 мая 2003 г.
Ученый секретарь диссертационного совета
д.т.н., профессор М.П. ЗАБРОДИН
Ю 8 О Актуальность работы
В связи с современным уровнем задач в области строительного материаловедения в качестве одной из основных может быть выделена проблема получения отечественных ячеистых строительных материалов -относительно недорогих, долговечных тепло- и экозащитных отечественных ячеистых бетонов. Из ячеистых автоклавных материалов на сегодня наиболее часто используются газобетоны, технологические линии для которых поставляются, в основном, из-за рубежа и которые являются достаточно дорогими. Однако ячеистый автоклавный бетон может быть представлен и современным пенобетоном, резательная технология и оборудование для создания которого с середины 90-х годов разрабатывается в ПГУПС совместно с НИПТИ «Стройиндустрия» (Москва). Ячеистый автоклавный пенобетон, полученный по резательной технологии, при сравнении с газобетоном оказывается более экономичным, что на сегодня сделало бы его более доступным для различных регионов России. Производство автоклавного пенобетона имеет свои технологические особенности получения на резательном переделе производства и резервы свойств, которые зависят, в том числе, и от твердой композиционной составляющей материала, включающей продукты превращения пенообразующих веществ.
Целью работы было получение и исследование свойств автоклавного пенобетона по резательной технологии, изготовленного на композиционной матрице. Для решения поставленной цели необходимо было решить следующие задачи:
— обосновать выбор состава кбмпозиционной матрицы для автоклавного пенобетона с учетом превращений пенообразующих веществ;
— исследовать получение автоклавного пенобетона и определить значения основных параметров; .
3 БИБЛИОТЕКА |
! С. Петербург , |
? ОЭ Щ Ш*т/0 }
— исследовать основные свойства автоклавного пенобетона резательной технологии;
— произвести экологический и экономический анализы материала;
— создать технологическую линию производства материала;
— освоить опытно — промышленное производство автоклавного
пенобетона.
Научная новизна работы состоит в следующем:
1. Предложен принципиально новый подход в улучшении теплозащитных свойств автоклавного пенобетона путем формирования композиционной матрицы за счет добавления к гидросиликатам высокомолекулярных соединений кальция, образующихся в процессах взаимодействия с пеной и, кроме того, веществ с высокими молекулярными массами, содержащимися в пене, в качестве которых наилучшими являются вещества на белок — содержащей основе.
2. Исследованы особенности достижения резательной прочности композиционной матрицы; установлено, что комплексная пенообразующая добавка способствует улучшению основных эксплуатационных характеристик автоклавного пенобетона.
3. С помощью метода адсорбции индикаторов (метода РЦА) показано, что автоклавный пенобетон обладает адсорбционной способностью по ионам тяжелых металлов, что делает его экозащитным.
4. Показано, что автоклавный пенобетон характеризуется однородной структурой с равномерным распределением пор по размерам.
Практическая ценность работы
1. С учетом представлений об особенностях природы составляющих композиционной матрицы получен модифицированный автоклавный пенобетон, характеризующийся при средней плотности 400-500-600 кг/м3 прочностью и морозостойкостью соответствующими требованиям ГОСТ 25485, а также пониженными на 15..20% теплопроводностью, на 25-35%
4
сорбционной влажностью и повышенным отношением Кизг^чж» рзвным 0,37…0,45.
2. Для пенообразующей добавки на протеиновой основе предложен модификатор, представленный солями жирных кислот, обеспечивающий повышение качества пены, выраженное в увеличении её кратности и устойчивости в цементном тесте, а также способствующий равномерному созреванию пенобетонного массива и повышению качества резки.
3. Разработаны основные параметры резательной технологии получения автоклавного пенобетона на композиционной матрице, выявлены зависимости параметров от температуры, времени выдержки массива, соотношения компонентов, исходного количества воды затворения.
4. Предложена технологическая схема получения автоклавного пенобетона, создано первое предприятие по выпуску автоклавного пенобетона производительностью до 7000 м3 в год, выпущены и испытаны опытные партии пенобетона.
5. Разработаны ТУ № 5743-002-01115840-2003 «Добавка в бетон пенообразующая «Ника»; ТУ № 5741-001-01115840-2002 «Блоки стеновые из ячеистого пенобетона», получено положительное решение от 24.
На защиту выносятся:
— обоснование выбора композиционной матрицы для автоклавного пенобетона, полученного по резательной технологии;
— параметры резательной технологии получения автоклавного пенобетона и технологическая линия получения материала;
— свойства автоклавного пенобетона, полученного по резательной технологии;
— экологический и экономический анализы получения и свойств материала;
Апробация работы
Работа докладывалась на международной конференции «Композит -2001», С-Петербург, 2001 г; на международном симпозиуме «Chelenger Concrete», Skotland, Dandee, 2002 г; на международных конференциях «Фундаментальные исследования в технических университетах», Санкт-Петербург, 2002 и 2003 г; на семинарах кафедры «Инженерная химия и защита окружающей среды» 2002-2003 г.
Объем диссертации: Диссертация изложена на 136 страницах, состоит из введения, 5 глав, списка использованной литературы из 101 наименования, 3-х приложений, 24 рисунков, 51 таблиц.
Содержание работы Основное количество опубликованных научных исследований за период последних 7-10 лет рассматривают материал, содержащий поры, в основном с точки зрения количества введенного газа (воздух или водород, соответственно пено- или газобетон), а также размеров и распределения пор, что обосновало возможность составления известных графиков зависимости прочности материала и (или) его теплопроводности от средней плотности. В развитие этих представлений с 1996-1997 гг. на кафедре «Инженерная химия и защита окружающей среды» ведутся работы по исследованию природы твердого скелета или иначе, твердой (каменной) составляющей ячеистого материала, которая, во-первых, несет основную эксплуатационную нагрузку и, во-вторых, сказывается на теплозащитных свойствах ячеистого материала в целом. Известные исследования автоклавных пеноматериалов во времени до примерно семидесятых годов прошлого века предоставляют основную информацию
6
о процессах превращения в автоклавах, оптимальных режимах запаривания, образующихся продуктах. Это научные труды школ Санкт-Петербурга и Москвы — профессоров П.И. Боженова, A.B. Волженского, A.B. Саталкина, П.Г. Комохова, известные научные школы Литвы, Эстонии, Магнитогорска (М.С. Гаркави), Алма-Аты (К. Куатбаев, Е. Естемесов, У. Махамбетова, Т. Солтамбеков). Именно эти работы послужили основой для постановки проблемы в работах кафедры «Инженерная химия и ЗОС» ПГУПС — какой по природе должна быть композиционная матрица ячеистого материала, что бы на этапе развития резательной технологии получения автоклавного пеноматериала обеспечить рациональные параметры технологии получения и свойства материала? При ответе на этот вопрос появляется дополнительная возможность управления свойствами материала с учетом природы композиционной матрицы (при прочих равных условиях пористости, распределения пор по размерам и др.), в том числе и одного из основных свойств материала — его теплопроводности. Проведенный анализ известных на сегодня зависимостей теплопроводности твердого каркаса, как части пористого пеноматериала, от природы слагающих этот каркас фаз показал, что теплозащитными свойствами композиционной каркасной структуры можно управлять, ориентируясь на значения молярных масс и энергосодержание составляющих композиционного материала. При этом, рассматривая фазы участвующих в реакции веществ и наполнители была выявлена тенденция взаимосвязи молярных масс веществ с теплозащитными свойствами композиционного материала на основе этих веществ, и показано, что чем более сложным является состав материала, выше мольные массы, ниже их энергосодержание, тем ниже значение коэффициента теплопроводности композиционной каменной составляющей пеноматериала (Л.Б. Сватовская). В таком случае одним из дополнительных резервов по свойствам композиционного материала
7
является такая природа вводимой пены, значения молярных масс для которой наибольшие и которая способна образовывать с составляющими неорганической смеси фазы сложного состава. В соответствии с классификацией строительных пен Хитрова A.B. (2000 г), наибольшей молекулярной массой обладает группа белок-содержащих ПАВ (V -группа), которая может быть описана приблизительной формулой: {—СН2 — СН2 — СН2 — CHN(Ch4)2 -СН2 -C00(Ch3)3S03} п, где п = 5… 10, и при п = 10 мольная масса продуктов 5-ой группы может достигать 3000 г/моль, т.е. наиболее высоких значений. Такого рода вещества должны обеспечить исходя из значений молярных масс повышенные теплозащитные характеристики каркаса. С другой стороны, щелочные соли жирных кислот, (III группа классификации) образующие с ионом Са2+ соединения с молярной массой более 600 г/моль, по схеме: Са2++2(С,5Н17СОО)—>Са(С15Н,7СОО)24 также могут быть рекомендованы композиционному материалу по показателям теплозащитности и гидрофобности. Исходя из этого, с учетом современного уровня знаний о природе теплозащитных свойств твердых тел в работе была принята в качестве наиболее рациональной композиционная матрица твердого каркаса с наибольшими молярными массами пенообразующих веществ. Используя известную формулу Кингери: ХсР = Х„(1 — VJ/(1 + Уд) была предварительно оценена ХсР твердой композиции; при этом как непрерывная фаза (\) в каркасе была рассмотрена гидросиликатная составляющая, с объемной долей 0,9 состава наиболее термодинамически обоснованого по значению величины -AG кДж/моль, а вводимая пена — как добавочная, Хд (табл. 1).
Таблица 1.
Параметры вводимых веществ.
Состав Свойства
Молярная масса, М г/моль Доля объема твердой части
Са(С|5Н,7СОО)2 606 0,02
{—СНг—СН2—СН2—СНЫ(СНз)2—€Н:~С00(СН:)з50з}ю 3000 0,08
Предварительный расчет показал, что Хср твердой композиции с пенодобавками понижается минимум на 0,02 Вт/(м-°С), что является обоснованием улучшения теплозащитных свойств автоклавного пенобетона.
В системе рассматриваемых знаний для того чтобы снижать теплопроводность твердого каркаса следует увеличивать объем пенообразующей добавки в смеси не только с точки зрения повышения количества вовлеченного пеной воздуха, но увеличения доли вещества с высокой молярной массой. Однако технологические особенности резательной технологии вносят свои коррективы в формирование массива — его резательному сопротивлению по прочности и его дальнейших строительно-технических свойств, поэтому в работе исследованы этапы получения пеноматериала автоклавного твердения, уточнён состав предварительной композиционной твердой матрицы, параметры резательного передела, а также строительно-технических и теплофизических свойств полученного материала. Проведенные исследования положены в основу создания производственной линии автоклавного ячеистого бетона.
Технологический процесс получения автоклавного пенобетона по резательной технологии включает: прием и подготовку сырьевых компонентов, приготовление ‘ячеисто-бетонной смеси, формование, выдержку и разрезание массива на изделия заданных размеров,
автоклавную обработку. Исследования показали, что качественная резка массива возможна при достижении им требуемой пластической прочности по всей высоте и периметру. Установлено, что на разрезание массива оказывают влияние следующие факторы: подготовка сырья; компонентный состав; условия перемешивания; поризация смеси; условия твердения массива.
Использовалось следующие сырьевые материалы: карьерный кварцевый песок месторождения «Келкова гора», размолотый до удельной поверхности =220 м2/кг, портландцемент ПЦ400 Д-20 ОАО «Пикалево» и известь Угловского месторождения. Химико-минералогический состав сырьевых материалов представлен в табл. 2.
Таблица 2
Химико-минералогический состав сырьевых материалов.
Наименов ание сырья Основные компоненты, мас.% Примечание
8Ю2 А12Оэ ИегОз СаО к2о + N320 БО/ См-
Песок ¿85% 5-7 0-1 следы следы следы след ы елел ы — Орг. примеси — следы.
Известь 5 1,5 1 ¿80 2 1,5 3,0 Время гашения 8-15 мин.
В начальный период созревания отформованная ячеистая масса может быть подвержена расслоению и осадке в результате нарушения структуры, особенно, для пенобетонов низкой плотности, имеющих недостаточную вязкость смеси. Это явление осложняет технологическую резку массива, проявляющееся в обрыве струн и его «обвале». Поэтому была определена целесообразная тонкость помола песка которая соответствует зависимости, представленной на рис.1
п 5
600
л
& 400 -
о
X
о 200
с; С
0
150 170 190 210 230 250 Зуд, м2/кг
. Рис.1. Взаимосвязь удельной поверхности песка и плотности пенобетона.
С целью улучшения качества пены и получения пенобетона на ее основе с улучшенными физико-механическими характеристиками в соответствии с высказанными ранее предположением в работе осуществлялась модификация пенообразующей добавки солями жирных кислот.
Исходная пенообразующая добавка имела следующие основные характеристики:
— внешний вид, оцениваемый визуально по просвету пробы -жидкость темно-коричневого цвета без посторонних включений;
— плотность, р=1080 кг/м3;
— концентрация ионов водорода в ед. рН=7,0…8,9.
Рабочий раствор пенообразующей добавки (ПД) приготавливался смешиванием ПД с водой (В) в соотношении: ПД:В=1:35.
Для модификации использовался 2% раствор стеарата калия, который добавлялся к рабочему раствору ПД и перемешивался до полного растворения всех компонентов. Пена из модифицированного рабочего
раствора пенообразующей добавки приготавливается в пеногенераторе при давлении 0,4 МПа. Полученные основные физико-технические характеристики пены представлены в табл.3.
Таблица 3
Характеристики пены, модифицированной пенообразующей
добавкой.
Пенообразую-щая добавка Модификатор Количество, мас.% Кратность, РПД Рпены Стойкость пены, сек. Куп пены в цементном тесте Вязкость пены, см
На протеиновой основе, р=1080 кг/м3 — — 12 18 0,8 16
-II- стеарат калия 5 13 21 0,86 13,6
-II- стеарат калия 10 14 26 0,92 12
стеарат калия 15 13,3 22 0,84 13
Установлено, что наилучшие характеристики имеет пена, полученная из рабочего раствора пенообразующей добавки (РПД), модифицированной (М) 2% раствором стеарата калия в соотношении: РПД:М = 90:10, где РПД раствор пенообразующей добавки состава: ПД:В=1:35 и М — модификатор, 2% раствор стеарата калия. На предложенный состав разработаны ТУ№ 5443-002-01115840-2003.
От природы и свойств пенообразующей добавки и образующейся пены на их основе, в конечном итоге, зависят физико-технические свойства пенобетона, формирование ячеистой структуры пенобетонного
массива и камня, включая степень поризации бетона, характер и размер пор, а также процесс гидратации цемента.
В связи с вышесказанным важной технологической задачей является определение оптимальных параметров пенообразования, поэтому следующим этапом исследований являлось определение оптимальной плотности пены для пенобетонов плотностью 400, 500 и 600 кг/м3. Для этого в цементно-известково-песчаный раствор вводилась пена разной плотности и была получена взаимосвязь оптимальной плотности пены и плотности пенобетона. Установлено, что уменьшение плотности пены ниже оптимального значения, приводит к коагуляции частиц портландцемента с образованием крупных агрегатов, наблюдаемых визуально. Увеличение плотности пены выше оптимального значения приводит к увеличению общего водо-вяжущего отношения поризованной массы, дополнительному водоотделению и расслоению пенобетонной смеси.
При формовании и стабилизации ячеистой структуры пенобетона особое значение приобретают факторы, обеспечивающие его равномерное созревание, к ним можно отнести пластическую прочность. Исследования показали взаимосвязь пластической прочности пенобетона с характером разрушения сырца во время резки. Установлено, что при высокой пластической прочности обеспечивается хорошая гладкая поверхность изделий, однако, при этом часто рвутся струны. При низкой пластической прочности достигается хорошее прорезание, но при этом не избежать слипания разрезанных изделий и разрушения массива. Установлено, что оптимальная пластическая прочность для используемого режима резания составляет 0,04…0,05 МПа.
Установлено также, что время достижения пластической прочности увеличивается при понижении средней плотности пенобетонных растворов. Для определения оптимального состава пенобетона проведены
13
подборы с учетом всех вышеуказанных особенностей изготовления массива и осуществления его резки. На первом этапе проведения подборов составов пенобетона определена оптимальная подвижность цементно-известково-песчаной растворной смеси, обеспечивающей максимальную прочность пенобетона. Подвижность растворной смеси определялась по вискозиметру Суттарда, полученные данные представлены на рис. 800 -1
600 400
£ « ? 1
£ £
¡5 200
с о
« 0 с
20
24
28
32
подвижность растворной смеси, см
Рис.2. Взаимосвязь плотности пенобетона и подвижности растворной смеси.
Проведенные подборы позволили определить оптимальные расходы материалов для пенобетонов средней плотности 400, 500, 600 кг/м3, которые представлены в табл.4. Твердение пенобетона осуществлялось в гидротермальных условиях при 1=174±5°С и давлении 8 атм. по уточненному режиму.
Таблица 4.
Оптимальный расход материалов для пенобетона Д400…Д600.
Средняя плотность, кг/м3 Расход материалов на 1 м3 бетона, кг В/ Вяж Подвижность растворной смеси по Сутгарду.см
Ц Известь П Вода в растворе Вода в пене ПД Объем пены, л
400 110 85 135 125 53,5 1,53 770 0,86 28
500 120 90 220 136 50,1 1,43 722 0,89 26
600 130 100 290 154 46,6 1,33 672 0,87 24
Прочность пенобетона определяли после окончания автоклавирования, а также в возрасте 28 и 56 суток. Для пенобетона, достигшего проектной прочности, определяли следующие физико-механические характеристики: прочность при изгибе, теплопроводность, паропроницаемость, сорбционную влажность, отпускную влажность, морозостойкость. Полученные данные представлены в табл. 5.
Таблица 5.
Основные физико-механические характеристики пенобетона Д 400.. .Д 600.
Средняя плотность, кг/м3 Класс по прочности на сжатие, поГОСТ 25485-89 Прочность при изгибе не менее, МПа Среднее значение КвДв Коэффициент теплопроводности, Вт/(м-°С) Сорбцион- ная влажность, %при относитель иой влажности 97% Морозостойкость по ГОСТ 25485,цик лы
400 В1-В1.5 0,7 0,45 0,08 7,5 -
500 В1-В2.5 0,7 0,40 0,10 8,4 15-35
600 В 1,5-3,5 0,9 0,37 0,11 9,0 15-75
Полученные результаты показывают, что пенобетон средней плотности 400, 500 и 600 кг/м3 имеет хорошую однородную поровую структуру, характеризуемую равномерным распределением мелких пор среди более крупных (рис. 3), имеет пониженную теплопроводность, прочность при сжатии и морозостойкость, что находится в соответствии с ГОСТ 25485, но при этом пенобетон имеет повышенный показатель
отношения КизгЖсж, свидетельствующий о повышенной
трещиностойкости бетона. Таким образом пенобетон рассмотренных составов при использовании белок-содержащей добавки, характеризуемой высокой молярной массой —до 3000 г/моль, модифицированной стеаратом калия, имеет пониженное значение коэффициента теплопроводности до 20% и пониженную примерно на 25% сорбционную влажность, по сравнению с ГОСТ, что согласуется с высказанным прогнозом о положительном влиянии на теплозащитность материала веществ с высоким значением мольной массы, к которым можно отнести ПД и продукты взаимодействия модификатора с ионами Са2+, представленные высокомолекулярными солями кальция, а также подтверждается положительное влияние щелочных солей жирных кислот на гидрофобность композиционного материала. На состав композиционного материала получено положительное решение по заявке 2002 112176/03(012658).
Рис.3. Поровая структура пенобетона Д600.
Анализируемые физико-механические характеристики пенобетона теплоизоляционного и теплоизоляционно-конструкционного явились основанием для разработки технических условий № 574Ь001-01115840* 2002 «Блоки стеновые из ячеистого бетона (пенобетона)» согласованных в
ГОССТРОЙ России, а также создания технологического регламента для производства по изготовлению блоков автоклавного твердения по резательной технологии.
Принципиальной особенностью технологии является приготовление в смесителе смеси из цемента, молотого песка, извести и воды с последующим введением в состав технической пены, полученной в пеногенераторе. Технологическая схема производства приведена на рис. 4.
Подобранные оптимальные составы обеспечивают такой набор пластической прочности массива, который достаточен для распалубки и разрезки изделий, разрезаемых вдоль и поперек оси формы струнами, длина которых превышает ширину массива на 100-г150 мм с каждой стороны.6 часов. Извлеченный из форм поддон с массивом при помощи захвата устанавливается на каретку резательного комплекса.
Рис.4 Принципиальная схема линии по производству изделий из автоклавного пенобетона по резательной технологии.
Каретка из исходного положения перемещается приводом на позицию поперечной резки, проходя через установку калибровки массива.
На позиции поперечной резки массив разрезается колеблющимися струнами в поперечном направлении. После завершения поперечной резки к массиву подходят упоры и каретка с массивом на поддоне проходит через струны продольной разрезки. Наличие подпорной стенки обеспечивает стабильное положение изделий при горизонтальной резке.
Схема резательного комплекса исключает образование трещин на массиве при продольной разрезке и обеспечивает точность резки в пределах ± 1 мм. После разрезки поддон с массивом устанавливается на автоклавную вагонетку. В цехе установлен автоклав 2×19м, в котором пенобетонные блоки подвергаются гидротермальному твердению при 1=174±5°С и давлении 8 атм.
На рис. 5 представлены фрагменты цеха и изделия из автоклавного пенобетона.
Проведенные физико-химические исследования показали, что после гидротермальной обработки основным продуктом гидратации является тоберморит, методом РЦА (распределение центров адсорбции, рис.6) установлено, что пенобетон гидротермального твердения способен адсорбировать ионы тяжелых металлов, например, ионы железа, доказывая, таким образом свою экозащитность.
с
Рис.З»
Фрагменты цеха по производству изделий из автоклавного пенобетона а — смеситель; б — резательный комплекс; в — выход готовой продукции из автоклава.
Рис.6. Распределение центров адсорбции на поверхности пенобетона автоклавного твердения.
ВЫВОДЫ
1. Предложено для улучшения теплозащитных свойств автоклавного пенобетона совершенствование композиционной матрицы путем добавления к гидросиликатам высокомолекулярных соединений кальция, образующихся в процессах взаимодействия с пеной и, кроме того, веществ с высокими молекулярными массами, содержащимися в пене, в качестве которых наилучшими являются вещества на белок — содержащей основе.
2. Исследованы особенности достижения резательной прочности композиционной матрицы, а прослежено, что использованная комплексная пенообразующая добавка способствует улучшению основных эксплуатационных характеристик автоклавного пенобетона.
3. Обнаружено с помощью метода адсорбции индикаторов — метода РЦА, что автоклавный пенобетон обладает адсорбционной способностью по ионам тяжелых металлов, что делает его одновременно экозащитным.
4. Исследована структура пеноматериала на композиционной матрице, показано, что пенобетон характеризуется однородной структурой с равномерным распределением пор по размерам.
2.1
5. С учетом представлений об особенностях природы составляющих композиционной матрицы получен автоклавный пенобетон, характеризующийся при средней плотности 400-500-600 кг/м3 прочностью и морозостойкостью в соответствие с ГОСТ 25485, а также пониженной на 15..20% теплопроводностью, пониженной сорбционной влажностью на 25..35% и повышенным ЯтоЖсж, равным 0,37…0,45.
6. Предложен для пенообразующей добавки на протеиновой основе модификатор, представленный солями жирных кислот, обеспечивающий повышение качества пены, выраженное увеличением её кратности и устойчивости в цементном тесте, а также способствующий равномерному созреванию пенобетонного массива и повышению качества резки.
7. Разработаны основные параметры резательной технологии получения автоклавного пенобетона на композиционной матрице, выявлены зависимости параметров от температуры, времени выдержки массива, соотношения компонентов, исходного количества воды затворения.
8. Предложена технологическая схема получения автоклавного пенобетона, впервые создано предприятие по выпуску автоклавного пенобетона производительностью до 7000 м3 в год по адресу Санкт-Петербург, ул. Предпортовая д.7; выпущены и испытаны опытные партии материалов.
9. Разработаны ТУ № 5743-002-01115840-2003 «Добавка в бетон пенообразующая «Ника»», ТУ № 5741-001-01115840-2002 «Блоки стеновые из ячеистого пенобетона», получено положительное решение от 24.01.2003 по заявке №2002 112 176 от 06.05.2002. Экономическая целесообразность материала состоит в прибыли до 20% на 1 м 3, экологическая — в защите от ионов тяжелых металлов.
гг.
Основное содержание работы опубликовано в следующих печатных работах и документах.
1. Мартынова В. Д. Об управлении свойствами автоклавного пенобетона. Сб. «Новые исследования в материаловедении и экологии». Вып.З СПб, ПГУПС, 2003г.
2. Сватовская Л.Б., Мартынова В. Д., Титова Т.С. Некоторые принципы создания защитных материалов и технологий. «Композит -2001» Тезисы докладов II межд. н.п. конф. «Защитные композиционные материалы и технологии третьего тысячелетия» СПб, 2001г.
3. Соловьева В.Я., Сычева A.M., Мартынова В. Д., Паутов П.А. Принципы создания добавок новых типов для твердения цементных смесей при пониженных и отрицательных температурах. Журнал «Сухие строительные смеси и новые технологии строительства» №1 2002г.
4. ., Мартынова В. Д., Хитров A.B., Петров С.Д. Новые резательные технологии производства автоклавного пенобетона. Журнал «Сухие строительные смеси и новые технологии строительства» №1 2002г.С -Петербург.
5. Svatovskaya L В., Martinova V. D. Design of mechanical-physical properties with considerations of the nature of introduced fillers and admixtures. International Congress «Challenges of concrete construction» 2002.
6. Мартынова В. Д., Латутова М.Н., Паутов П.А. Пенобетоны для монолитного домостроения и теплоизоляционные растворы. Бетон и железобетон в третьем тысячелетии. II международная научно-практическая конференция Ростов-на-Дону 2002г.
7. Сватовская Л.Б., Мартынова В. Д., Титова Т.С. Концепция
использования изменения энергосодержания системы для создания
экозащитных материалов и технологий. Фундаментальные
исследования в технических университетах. Материалы VI
23
Всероссийской конференции по проблемам науки и высшей школы.-СПбГПУ 2002г.
8. Хитров A.B., Мартынова В. Д., Петров С.Д. Поведение пенообразователей при низких температурах и их взаимодействие с противоморозными добавками. Сб. «Новые исследования в материаловедении и экологии». Вып.2 СПб, ПГУПС, 2003г.
9. Хитров A.B., Мартынова В. Д., Верховская Ю.М. Пенообразующая добавка на комплексной основе для монолитного домостроения. Сб. «Новые исследования в материаловедении и экологии». Вып.2 СПб, ПГУПС, 2003г.
Ю.Решение о выдаче патента. № 2002112176/03(012658).
11.ТУ №5741 — 001-01115840-2002, «Блоки стеновые из ячеистого бетона (пенобетона)»
12.ТУ №5743-002-01115840-2003, «Добавка в бетон пенообразующая «Ника»».
Подписано к печати Печать — ризография. Тираж 100 экз.
Тип.ПГУПС
26.05.03г. Печл. 1.5
Бумага для множит.апп. Формат 60×84 1\16
Заказ № 54%.
190031, С-Петербург, Московский пр., 9
г
!
»
»
ь
I
P108Ü г
2QO<Í-A
logc>£
Виды железобетонных изделий для промышленного и гражданского строительства.
Бетонные изделия, объединяющие в себе свойства металла и бетона, носят название железобетона. Плюсы от бетона и от железной арматуры отражаются на показателях сжатия (бетон имеет высокие показатели сопротивления сжатию) и растяжения (стальная арматура хорошо работает при нагрузках растяжения).
Конструкции из железобетона бывают двух видов по способу изготовления:
1. Монолитные Монолитные железобетонные конструкции возводят на тех местах, где данная конструкция и будет расположена в дальнейшем без изменения местоположения. При создании подобных конструкций производятся индивидуальные расчеты и тратятся большие усилия рабочих по созданию нестандартного объекта.
2. Сборные. Сборные железобетонные конструкции намного удобнее при строительстве и значительно экономичнее. Созданные на специализированных заводах по общепризнанным стандартам и имея конкретные характеристики, из расчета которых можно планировать дальнейшее строительство, естественно, пользуются большим спросом.
По назначению Сборные ЖБИ подразделяются на:
1. Изделия для жилых и гражданских зданий.
2. Изделия для инженерных сооружений.
3. Изделия для промышленных зданий.
4. Другие изделия различного назначения.
В наше время бетонные и железобетонные изделия применяются во всех сферах строительства. Классифицируются такие изделия по типу бетона, объемному весу, способу армирования, конечному назначению и другим признакам.
Железобетонные изделия для жилых и гражданских знаний
При строительстве жилых и гражданских зданий применяются различные ЖБИ, классифицирующиеся для строительства:
1. Каркасов зданий.
2. Фундаментов и подземных частей зданий.
3. Стеновых блоков и панелей.
4. Междуэтажных перекрытий.
5. Лестниц.
Отделка лицевой поверхности железобетонных изделий
Может предполагать механическую обработку, обнажение поверхности заполнителей химическим способом, облицовку плитками и плитами, нанесение разнообразных дробленых материалов, поверхностное или дробленое окрашивание, металлизацию, огневую, высокотемпературную (плазма) и др. обработку
Большие эстетические возможности ж/б с использованием разнообразных решений по цвету, фактуре и текстуре материала. Архитектору принадлежит ведущая роль в в решении этих проблем, в развитии новых архитектурных форм.
III изделия на основе вяжущих
Силикатный кирпич и силикальцитные изделия
Силикатный кирпич состоит из кварцевого песка и извести.
Технические характеристики:
предел прочности силикатного кирпича при сжатии должен быть не менее 15-20 МПа.
Плотность не должна быть меньше 1300 кг/м³.
Также есть параметр морозостойкости кирпича. Эта цифра представляет из себя количество заморозок и разморозок, которые гарантированно выдержит силикатный кирпич.
температура применения: она не должна быть больше 550 °C.
Силикальцитные изделия, значительно превышают прочность бетонных изделий (800..1000 кг/см2), что позволяет применять его в самых сложных конструкциях. Объемный вес газосиликальцита (200..300 кг/м3) раскрывают большие перспективы его использования в качестве теплоизоляционного материала.
Как присутствие кремнезема в строительных материалах повлияет на мою сделку с коммерческой недвижимостью?
Недавно я получил запрос от клиента, желающего провести Фазу I экологической оценки объекта (ESA) для здания, которое они собирались купить. ЕКА, которую они хотели, включало в себя обычный список опасных загрязнителей, к которым я привык видеть за долгие годы: асбест, свинцовая краска и радон. Однако этот список также включал опасный материал, которого я раньше не видел в списке ESA фазы I: кремнезем.Кремнезем содержится в сотнях строительных материалов, с которыми мы сталкиваемся в повседневной жизни, таких как бетон, кирпич, строительный раствор, керамическая плитка, раствор, краски и т. Д. Хотя присутствие кремнезема в строительных изделиях вряд ли может вызывать беспокойство. текущие сделки с коммерческой недвижимостью, недавние изменения в законодательстве и возможные будущие изменения могут повлиять на будущие сделки. Следовательно, заинтересованным сторонам в сфере коммерческой недвижимости лучше всего ознакомиться с кремнеземом, связанными с ним опасностями и тем, как недавние изменения регулирования могут повлиять на их бизнес в будущем.
Кремний — это природный минерал, содержащийся в скалах, почвах и песках по всему миру. Это один из самых распространенных минералов на планете, составляющий более девяноста процентов земной коры. Поскольку диоксид кремния настолько распространен в окружающей среде, он нашел широкое и многоцелевое использование в нашей повседневной жизни. Он содержится во многих бытовых чистящих средствах, глиняной и керамической посуде, тальке, косметике и является обычным наполнителем, используемым в красках, пластмассах и каучуках. Он также содержится в обычных строительных материалах, таких как гравий, бетон, кирпич, строительный раствор, растворы, керамическая черепица, черепица, штукатурка и т. Д.Нарушение этих материалов во время строительных или ремонтных работ может привести к образованию пыли с частицами кремнезема, что может представлять потенциальную опасность для строительных рабочих и / или служащих в прилегающих районах.
Многократное чрезмерное воздействие вдыхаемой кварцевой пыли может вызвать множество различных заболеваний; наиболее распространенным является силикоз, прогрессирующее неизлечимое заболевание легких. Силикоз чаще всего встречается в профессиях, где воздействие диоксида кремния чрезвычайно велико, например, при пескоструйной очистке, горнодобывающей промышленности, строительстве туннелей, литейных цехах и бетонных / кладочных работах.Продолжительное воздействие вдыхаемого кремнезема на рабочем месте также связано с раком легких, заболеванием почек и хронической обструктивной болезнью легких.
В настоящее время диоксид кремния регулируется только в США Управлением по охране труда (OSHA). OSHA недавно обновила свой стандарт на диоксид кремния, значительно снизив уровень содержания в воздухе диоксида кремния, которому могут подвергаться рабочие. Изменения существенно повлияют на то, сколько работодателей и сотрудников работают с материалами, содержащими диоксид кремния, и сталкиваются с ними.Такие методы работы на рабочем месте, как обработка водяным туманом или местная вытяжная вентиляция для уменьшения количества пыли во время сверления, резки, шлифования и т. Д., Станут обычным явлением. Если эти методы контроля не могут снизить воздействие, использование респираторов может стать обязательным. Эти изменения повлияют на стоимость проектов строительства и / или реконструкции, поэтому наибольшее бремя, связанное с воздействием кремнезема, ляжет на подрядчиков. Эта повышенная стоимость неизбежно перекладывается на владельца здания.Следовательно, проекты строительства и ремонта могут стать дороже в будущем. В настоящее время, похоже, не стоит ожидать проведения комплексных проверок на содержание кремнезема в строительных материалах.
Преимущества промышленного строительного камня из силиката кальция — Masonry Magazine
Искусственный камень
Синди Лусмор
Дом, построенный из Камня Теней Аррискрафта.Хотя кирпичи из силиката кальция (CSMU) не новы, их уникальные качества и преимущества, возможно, сегодня более актуальны, чем когда-либо.Понимание того, чем CSMU отличается от другого производимого камня, раскрывает важные преимущества этого продукта для каменной кладки.
CSMU — это изделия из искусственного камня, обладающие исключительной прочностью и долговечностью, а также замечательной аутентичностью с точки зрения текстуры и внешнего вида. Arriscraft из Онтарио, Канада, производит строительный камень из силиката кальция более 60 лет. Этот тип искусственного камня отличается как от глиняного кирпича, так и от изделий из бетонной кладки.
Как оно сделано
Природные материалы смешиваются, а затем прессуются в блоки модульного размера под высоким давлением.Затем блоки подвергаются воздействию паровой системы с тщательным контролем, чтобы получить кирпичную кладку с однородной мелкозернистой текстурой. Эта технология Natural Process® (запатентованная Arriscraft) воспроизводит процесс образования камня в земле, за исключением более быстрого. Во время производственного процесса сырье химически реагирует с образованием связующего на основе гидрата силиката кальция, в результате чего образуются прочные, прочные и неразрывно связанные блоки.
Хотя этот производственный процесс очень мало изменился за десятилетия, спрос на этот камень из силиката кальция на естественной основе продолжает расти.Эти «зеленые» компоненты полностью натуральные, за исключением пигментов, добавляемых по мере объединения сырья. Такое смешивание создает кирпичную кладку с сквозным цветом тела, поэтому камни можно резать, придавать им форму, точить вручную или обрабатывать на месте, сохраняя при этом мелкозернистую текстуру и цвет.
Работает как добытый камень
Поскольку CSMU созданы в виде натурального камня, добытого в карьерах, они обладают такими же преимуществами прочности и долговечности. Продукция Arriscraft Building Stone предлагается с пожизненной гарантией и не выцветает, не усаживается, не трескается или не стареет, как изделия из камня, изготовленные из бетона, особенно в суровых погодных условиях.Эти продукты из силиката кальция соответствуют стандарту ASTM C73-99a, который определяет требования к прочности на сжатие и абсорбции для того, чтобы материал был классифицирован как умеренный или тяжелый.
Стандарты продуктов на основе цемента не распространяются на CSMU; в рамках стандартов силиката кальция нет требований к характеристикам в отношении устойчивости к замораживанию / оттаиванию. Принято считать, что долговечность кладки из силиката кальция тесно связана с ее прочностными свойствами.Каменные изделия Arriscraft прошли независимые испытания, чтобы гарантировать, что они соответствуют и превосходят требования к суровым погодным условиям ASTM C73.
Широкий выбор стилей
Хотя добытый камень, очевидно, нельзя изменить по цвету, форме и профилю, CSMU производятся в широком спектре конструкций, предлагая строителям двойное преимущество: производительность и стиль.
По словам менеджера по маркетингу Arriscraft Марты Зонневельд: «Даже клиенты, которые знают нас на протяжении десятилетий, иногда с удивлением узнают о нашей полной линии.Они часто влюбляются в один стиль камня, я полагаю, из-за повторяющихся типов проектов. Некоторые знают нас благодаря нашему традиционному камню, возможно, как строители домов, в то время как другие предпочитают архитектурный дизайн для коммерческих или институциональных проектов ».
Ассортимент продукции охватывает диапазон от исторических до современных, удовлетворяя не менее широкий спектр строительных конструкций — от университетских зданий старого мира до ультрасовременных домов. В настоящее время Arriscraft предлагает 10 стилей строительного камня в дополнение к Renaissance® Masonry Units и серии продуктов Thin-Clad.
Настройка цвета и перехода
В то время как большинство производимых изделий из камня предлагают широкий выбор стилей и цветов, уникальный производственный процесс Arriscraft открывает возможности для индивидуальной настройки. Поскольку пигменты CSMU добавляются во время процесса, запуск каждого продукта может отличаться без каких-либо изменений в настройке. Эта гибкость, а также специальная техническая лаборатория сделали индивидуальные заказы очень распространенными в Arriscraft.
Пример использования: Университет Вайоминга
University of WyomingУниверситет Вайоминга хотел включить свой исторический песчаник местного происхождения в дизайн нового, ультрасовременного здания Marian H.Центр Рошель Гейтвей. Однако, когда региональный карьер был закрыт, университет изо всех сил пытался найти подходящий вариант «натурального» камня в их фирменных цветах.
Arriscraft работал с университетом и дизайнерами над созданием нестандартного узора связи с использованием стандартных цветов каменной кладки эпохи Возрождения. По словам Чета Локкарда, руководителя проекта в Project Guide Services, «Arriscraft смогла выбрать нужный нам цвет. Мы хотели создать больше впечатлений от Gateway Center, и у него большой выбор стандартных цветов, что также позволило сэкономить деньги на проекте.Лучшее в Arriscraft — это то, что он ничем не отличается от камня, добытого в карьере, но имеет более однородный цвет ».
Пример использования: Технологический институт штата Вирджиния
Virginia TechОснованный в 1896 году, Virginia Tech имеет богатую и уникальную историю. Чтобы сохранить источник камня «хоки», учреждение пошло так далеко, что приобрело карьер в 1970-х годах. Но с истощением запасов (ход карьеров фактически менялся) администраторы столкнулись с ограниченным запасом.
В тесном сотрудничестве со школой специалисты Arriscraft воссоздали узор камня Хоки, используя строительный камень Камберленд и создав индивидуальную цветовую смесь «Серый Рокпорт».Вторая смесь включает 4–5 процентов легендарного черного камня, добытого в Вирджинском технологическом институте, для наиболее выдающихся проектов. Основная смесь Rockport Grey используется в университетских зданиях, коммерческих зданиях, связанных со школой, и даже некоторыми выпускниками для своих резиденций, поскольку они так тесно отождествляют себя со своей альма-матер.
Историческое соответствие
Поскольку кирпичи из силиката кальция имеют аутентичный, естественный вид, они также являются лучшим кандидатом для использования в исторических проектах, будь то ремонт и реконструкция, или новые конструкции, интегрируемые со старыми зданиями.Благодаря дополнительному преимуществу сочетания цветов строительный камень Arriscraft может быть невероятно близок к идеальному сочетанию.
Пример использования: Университет Майами
Университет МайамиУниверситет Майами в Огайо, основанный в 1809 году, является одним из старейших университетов страны. Поскольку требовались новые здания, школе требовалась более эффективная и экономичная альтернатива добытому камню.
Компания Arriscraft разработала особый цвет своего строительного камня для фрески, чтобы создать почти идеальный цвет для оригинального камня начала 19 века, который использовался в кампусе.Хотя камень Arriscraft был на самом деле дороже камня, добытого в карьере, сроки проекта и затраты на установку были значительно сокращены, что позволило сэкономить сотни тысяч долларов на проекте.
Стандартная и упрощенная установка
Как промышленный продукт, Arriscraft Building Stone разработан для установки с использованием стандартных методов кладки, независимо от стиля камня. Однако, в то время как некоторые стили строительного камня требуют соблюдения рисунка скрепления, Arriscraft представила новые варианты, предназначенные для более быстрой установки.
Поразительно простой, Urban Ledgestone — первый продукт Arriscraft, предназначенный для укладки по курсиру. Чтобы добиться этого рисунка, укладывают камень одного размера в один или несколько рядов, за которыми следуют один или несколько рядов второго размера.
Представленный в 2015 году Matterhorn Building Stone отличается простым в установке двухуровневым узором скрепления. Маттерхорн на 99 процентов изготовлен из вторичного материала существующих производственных процессов.
Новинка 2016 года, 32-дюймовый каменный блок Evolution Masonry Unit — самый длинный каменный продукт Arriscraft. По заявлению компании, проектировщики зданий проявили большой интерес к более длинному камню, и они смогли модернизировать существующую производственную технологию, чтобы приспособить производство этой большой каменной кладки.
Для получения дополнительной информации посетите www.arriscraft.com.
Синди Лусмор — писатель-фрилансер, с ней можно связаться по адресу cindyloosemore @ rogers.com.
Что такое плита из силиката кальция? | Фиброцемент | Фиброцементная плита | Кровельный лист из волокнистого цемента | Фиброцементная плита
Кальциево-силикатная плита как новый экологически чистый строительный материал, который имеет превосходные огнестойкие характеристики и сопротивление приливу, за исключением традиционных гипсовых панелей, выполняющих функции снаружи, и имеет сверхдлительный срок службы. Применение: бизнес-инженерные сооружения потолка и стены, семейная отделка, и мебель из вагонки, и рекламная марка вагонки, и корабль через складской борт, и склад из навесной доски, и сетевой пол и туннель, внутренняя инженерия стены. Доска.
Классификация:
-Термоизоляционные плиты из силиката кальция
Изоляционная плита из силиката кальция, называемая силикатом кальция с микропорами, который представляет собой белый твердый новый изоляционный материал с легкой плотностью, высокой прочностью, низкой теплопроводностью, высокой термостойкостью, Устойчивость к коррозии, возможность резать, пилить и т. д.
Кальциево-силикатные плиты широко используются в электроэнергетике, металлургии, нефтехимии, строительстве, на кораблях и другом оборудовании в области изоляции труб, стен и крыш, а также противопожарной изоляции.Толщина обычно превышает 30 мм, плотность 200-1000 кг / м3.
— Плита из силиката кальция для декора
Доска для отделки из силиката кальция была изобретена компанией OCFG в Соединенных Штатах, которая представляет собой новый строительный лист, характеристики которого в целом известны во всем мире, в 1970-х годах 20-го века были разработаны страны способствуют использованию и развитию. Европа, Америка, Япония, а также Австралия и Тайвань являются наиболее распространенными странами и регионами, использующими силикат кальция. заявление.Толщина 4-20мм, 1220 * 2440мм ориентированный аспект. В то время как большие плиты из силиката кальция в декоративных потолках из силиката кальция, их огнестойкие разновидности и другие преимущества широко используются в потолках
Связанные 4
OCT
Руководство по выбору материалов из кремнезема, кварца и силиката
Кремнезем, кварц и силикатные материалы включают плавленый кварц, кварц, каолин или материалы на основе глины, кордиерит, стеатит, форстерит, силлиманит, циркон, фарфор и шамот.Они основаны на диоксиде кремния и различных химических вариациях.
Переработка и производство
Кремнезем и силикатные материалы плавятся или отливаются с добавками оксидов алюминия, кальция, натрия и магния для изменения определенных свойств и придания различных технологических характеристик. Кварц — твердый кристаллический минерал, который является вторым по распространенности минералом в земной коре. Он часто окрашен примесями, но также содержит диоксид кремния.
Химические вариации и различные методы обработки могут использоваться для улучшения прозрачности, прозрачности и диэлектрических свойств кремнеземных и силикатных материалов.Эти различные методы используются для производства силиката алюминия, силиката кальция, глины, кордиерита, шамота, форстерита и каолина.
Типы материалов
База данных Engineering360 SpecSearch содержит информацию об этих и других типах кремнеземных и силикатных материалов.
Силикат алюминия нерастворим и часто используется в качестве огнеупора при производстве стекла. Категории включают силлиманит, фибролит и слюду (мусковит, биотит и флогопит). Слюда является огнестойкой и негорючей, имеет низкую теплопроводность, отличную термическую стабильность и хорошие диэлектрические или электроизоляционные свойства.
Кордиерит имеет низкий коэффициент теплового расширения, высокую механическую прочность, низкие диэлектрические потери и отличную термостойкость. Он может выдерживать красный нагрев до охлаждения ледяной водой, а затем снова возвращаться к красному огню. Кордиерит часто превращается в изолятор или изолирующую подложку из-за его хороших диэлектрических свойств.
шамот представляет собой термостойкую вторичную глину или смесь на основе глины, пригодную для применения при повышенных температурах или при применении огнеупорных связующих.В огнеупорах или керамике на основе шамота используется натуральная глина или смесь глины и другой керамики, такой как оксид алюминия, алюминат кальция или карбид кремния.
Форстерит представляет собой стехиометрический ортосиликат магния (Mg 2 SiO 4 ), используемый в приложениях, требующих высокого коэффициента теплового расширения. Форстерит имеет желаемые электроизоляционные свойства и используется в качестве слоя на листах трансформаторной стали.
Плавленый кремнезем представляет собой соединение кремния и кислорода.Аморфный плавленый кварц высокой чистоты — это высокопроизводительная керамика с очень низким расширением, замечательной стойкостью к тепловому удару, низкой теплопроводностью, отличной электроизоляцией до 1000 ° C и отличной устойчивостью к коррозии от расплавленного металла и стекла.
Стеатитовая керамика используется для изоляции высоких частот, низких потерь и высокого напряжения. Стеатит обладает хорошими механическими свойствами и низкими электрическими потерями. Он используется в воспламенителях, стойках, ограничителях перенапряжения, формах катушек, прокладках и свечах зажигания.Стеатит легко производить с жесткими допусками и намного дешевле, чем керамические изоляторы из оксида алюминия.
Приложения
Кремнезем, кварц и силикатные материалы используются в оптических, термических, химических, электрических и электронных устройствах.
Кредит изображения:
geo.umn.edu
Характеристики карбонизации силиката γ-дикальция для низкоуглеродистого строительного материала
Основные характеристики
- •
γ-C 2 Блоки S демонстрируют быстрое увеличение прочности с высокой способностью абсорбировать CO 2 .
- •
Увеличение объема твердой фазы уплотняет матрицу и обеспечивает высокую прочность.
- •
Ca 2+ Диссоциация ионов ускоряется CO 2 .
- •
Продукты с высоким содержанием кальция и кремния имеют тенденцию расти в кластерах по отдельности.
Abstract
Силикат γ-дикальция (γ-C 2 S) характеризуется высокой реакционной способностью к карбонизации и имеет потенциал для использования в качестве строительного материала с дополнительным преимуществом связывания CO 2 .В настоящей работе рассматриваются характеристики формованных под давлением образцов γ-C 2 S, подвергнутых ускоренному карбонизационному отверждению, включая изменения в микроструктуре, степени карбонизации и механической прочности. Результаты показывают, что механическая прочность и поверхностная плотность карбонизированного блока γ-C 2 S хорошо коррелируют со степенью его карбонизации, что объясняется образованием более объемных продуктов карбонизации. Это укрепляет структуру и уплотняет матрицу.Продукты карбонизации включают кальцит в качестве основной морфологии и арагонит в качестве второстепенной фазы и аморфный силикагель, модифицированный кальцием, образованный координированными тетраэдрами SiO 4 . Измерение проводимости и концентрации ионов выявляет ускоренное растворение ионов Ca 2+ в присутствии CO 2 является причиной высокой реакционной способности γ-C 2 S при карбонизации. Предложена концептуальная модель процесса карбонизации, основанная на распределение Ca-модифицированного силикагеля и карбонатов кальция.Кроме того, экологическая оценка показывает, что γ-C 2 S, как мы надеемся, сократит 40% выбросов CO 2 по сравнению с обычным цементом, что открывает новую область применения нового низкоуглеродистого строительного материала.
Ключевые слова
Силикат γ-дикальция
Ускоренная карбонизация
Карбонат кальция
Силикагель, модифицированный кальцием
CO 2 эмиссия
Рекомендуемые статьи Цитирующие статьи (0)
Просмотреть полный текст© 2018 .
Рекомендуемые статьи
Цитирующие статьи
(PDF) Строительный материал из силиката кальция — препарат и свойства
МЕЖДУНАРОДНАЯ КОНФЕРЕНЦИЯ IMS / 4 ПО ПРИМЕНЕНИЮ
ТРАДИЦИОННЫХ И ВЫСОКОЭФФЕКТИВНЫХ МАТЕРИАЛОВ ДЛЯ ТРУДОВОЙ ОКРУЖАЮЩЕЙ СРЕДЫ
— 25 марта 2000 г. 2010
Строительный материал из силиката кальция — подготовка и
Свойства
ДИМИТАР ГЕОРГИЕВ1, БОГДАН БОГДАНОВ1, ЯНЧО ХРИСТОВ1,
ИРЕНА МАРКОВСКА1, АРЕНА МАРКОВСКА1,
ИРЕНА МАРКОВСКА1, КРАНА МАРКОВСКА1 Университет Ассена Златарова,
1 Проф.Якимова, 8010 Бургас, Болгария. e-mail: dgeorgiev@btu.bg
2 Кафедра химического машиностроения, Американский университет Шарджи, ОАЭ
Резюме Спрос на альтернативные строительные материалы и их качество теперь является ответственной задачей
, в которой необходимо решить проблемы, связанные с технологические, экологические и экономические
соображения. Целью данной работы является получение силикатно-кальциевого материала для нужд строительства
.Цель ограничивается разработкой соответствующих составов силикатного материала кальция
, отработанного в технологических условиях, для его синтеза в лаборатории. Получение
конструкционного материала силиката кальция осуществляется методом гидротермального синтеза
. Исследованы основные физико-механические свойства материала.
Ключевые слова силикат кальция, белый кирпич, гидротермальный синтез
1. Введение
Поиск альтернативных высококачественных строительных материалов продолжается и представляется сложной задачей
, которая должна решить одновременно несколько проблем технологического, экологического
и экономический характер.Эта статья представляет возможность подготовить и охарактеризовать строительный материал из силиката кальция-
.
Силикат кальция известен силикатным технологам как «искусственный камень», внешний вид и свойства которого
очень близки к натуральным камням. Этот материал использовался в течение
долгое время для изготовления кирпича, плитки, облицовки стен и т. Д. [1-3]. В течение некоторого времени кирпич
, произведенный из силиката кальция, более широко известен как «силикатный кирпич» или «белый кирпич».
Последнее название происходит от естественного белого цвета силиката кальция.
Материал имеет отличные характеристики на разрыв, хорошую термическую стойкость и звукоизоляционные свойства.
. Главный недостаток — высокая водопроницаемость и водопоглощение.
Следовательно, если они используются для наружных стен, они должны быть покрыты водонепроницаемыми и теплоизоляционными слоями
[1-3].
Целью данной статьи является проведение исследований по получению силикатно-кальциевого материала
для строительной промышленности.Исследования были нацелены на разработку подходящего кальциевого шпателя
Trades Supply — камня из силиката кальция
Камень из силиката кальция
Кладки из силиката кальция (искусственный песчаник) доступны в следующих типах продуктов: 1) Полнослойные блоки (блоки Renaissance Stone), которые по внешнему виду и физическим свойствам очень похожи на известняк и песчаник Индианы, размером 4x4x24, 4х8х24 и 4х12х24; 2) строительный камень («Цитадель», «Старая мельница» и «Лорье») обеспечивает отличную экономичность для двух- и трехуровневого тесаного камня; эти блоки строительного камня, уложенные на несущую полку, устанавливаются по цене ниже цены наклеенного камня с гарантией того, что материал никогда не упадет со здания; и 3) плитка (ArrisTile), ¾ ”блоки Renaissance Stone для внутренних работ, которые можно приклеивать к любому основанию, чтобы придать вид сплошных известняковых блоков, отлично подходящих для проектов реконструкции и модернизации.
Предлагаемое использование
- Дымоходы
- Камины
- За дровяными печами
- Внешние подъезды
- Фасад дома
- Наружные стены